
Is preventive maintenance important for your company?
Preventive maintenance may seem basic at first, but according to statistics, 55% of companies still practice corrective maintenance methods. This is a good practice, as your building's systems will work until a problem or breakdown occurs. However, it is recognized that this type of maintenance results in much higher operating costs for a company.
What is preventive maintenance?
Preventive maintenance is an essential process to ensure the smooth running of your business. It is an operation that combines monitoring and preventive maintenance of your material and equipment. Preventive maintenance, or planned technical maintenance, consists in intervening on equipment at regular intervals or according to predefined criteria. Its primary objective is to reduce the risk of breakdowns on goods, machines and equipment, but it also allows to reach more general objectives. This is why most factories and companies are looking to increase the amount of preventive maintenance they implement compared to corrective maintenance.
What is the purpose of preventive maintenance?
The main purpose of preventive maintenance is to limit the risk of breakdowns and to reduce the number and frequency of machine breakdowns. It is therefore useful to :
- Reduce the frequency of production stops
- Reduce machine downtime for repairs
- Increase the life span of machines and equipment
- Plan corrective maintenance interventions to offer better conditions
- Better manage spare parts inventory
- Avoid unnecessary consumption of energy, lubricants and consumables
- Reduce the maintenance budget
- Improve the working conditions of the personnel
- Limit or even eliminate the causes of serious accidents.
Why is it important?
Downtime is one of the biggest money losers for companies. The importance of implementing preventive maintenance is that it allows businesses to continue to operate continuously without the risk of unplanned downtime. Reducing downtime increases productivity and improves your company's profitability.
Regular maintenance of your equipment also reduces the risk of equipment failure or costly repairs. Through maintenance, you can keep your equipment in good condition and extend the life of your machines.
There are 2 types of maintenance; preventive and corrective. What is the difference between the two?
Why solve problems when they occur when you can prevent them? Corrective maintenance allows you to solve problems while preventive maintenance seeks to avoid them. Thus, corrective maintenance, sometimes divided into palliative and curative maintenance, is performed only when a breakdown occurs on a machine or equipment. Preventive maintenance, on the other hand, seeks to verify that a machine is working properly and to identify any faults in its operation before it breaks down, by means of routine checks and tasks.
What are the different types of preventive maintenance?
There are 3 types of preventive maintenance:
- systematic maintenance
- conditional maintenance
- predictive maintenance.
Systematic maintenance
Systematic preventive maintenance is performed at pre-established time intervals or according to a defined number of usage units, but without prior control of the machine's condition. It concerns the first stages of degradation on a piece of equipment. It can be carried out at predefined intervals, or according to a criterion of use, without taking into account the conditions of use of the machine.
This type of maintenance requires a good knowledge of the degradation rules. It must be carried out in a reliable way, so as to eliminate any need for additional checks between two interventions or to avoid additional monitoring outside the inspection periods.
It is generally inexpensive. The only drawback is the need to determine the ideal frequency of part replacement. Here are some examples: Changing oil, bearings, seals, springs, contacts, resistors, lamps. Adjustment of tension, belts, pressure, potentiometers. Control of levels, torque, tightening, etc.
Conditional maintenance
The conditional maintenance is based on a monitoring of the machine operation and/or of the significant parameters of this operation including the actions which result from it (pressure, level, flow, etc). The results of these controls are planned for industrial maintenance operations. This type of maintenance makes it possible to overcome the disadvantages of systematic maintenance. It does not require any additional knowledge, except for the comparison of the controls with the predefined thresholds. It can be continuous with a permanent recording of the parameters measured, or discontinuous with a periodic measurement of these parameters.
Predictive maintenance
Forecast maintenance, also called predictive maintenance, is designed to help determine the condition of equipment in service in order to estimate when maintenance should be performed. This approach promises cost savings over routine or time-based preventive maintenance because tasks are performed only when warranted. Thus, it is considered condition-based maintenance performed as suggested by estimates of an element's degradation state. It is particularly useful for preventing unexpected equipment failures, increasing plant safety, reducing accidents with a negative impact on the environment and optimizing spare parts management.
Predictive maintenance differs from preventive maintenance in that it relies on the actual condition of the equipment, rather than average or expected life statistics, to predict when maintenance will be required.
Now, if you want to implement a preventive maintenance system in your business, the GraceSense™ predictive maintenance system could be a very good solution for your business.
The GraceSense™ predictive maintenance system is an asset condition monitoring system that uses integrated wireless sensor technology. Advanced data analytics provide asset managers with in-depth information about machine health to effectively prioritize resources and maximize the value of their maintenance spend. GraceSense™ technology improves reliability, safety and maintenance metrics by remotely monitoring equipment health and sending preemptive notifications via SMS or email alerts with preconfigured, step-by-step remediation instructions when abnormal behavior is detected.
It has a cost-effective wireless condition monitoring solution that can provide real-time, sensor-based insight into almost any industrial application. The collected information can be leveraged to assist in decision making provided in the cloud via WiFi or LTE and/or in the PLC via Ethernet/IP or Modbus TCP/IP. The simple and intuitive web application combined with secure data storage provides unlimited possibilities for data retrieval, visualization, analysis and reporting. As a result, worker safety is improved by reducing unplanned corrective maintenance activities.
Among the system components that may be useful to your installation;
The PANEL-MOUNT™ Node is a cost-effective solution for integrating wired third-party sensors via 0-10V, 4-20 mA, as well as serial communications via RS485 from devices such as cell phones, laptops, desktops, etc. Wireless Sensor Nodes can monitor vibration and temperature to insightfully assess the health of rotating equipment, multiple mounting options ensure rapid deployment in applications across all industries. The batteries are easy to replace and offer a life span of 3 to 5 years, depending on usage.
The system also features 3 types of gateways CLOUDGATE™, CONTROLGATE™, COMBOGATE™ that can transfer information accumulated on field nodes to a troubleshooting platform that can be operated via the Cloud Maintenance Hub and/or your own platform.
CloudGate™ transfers information from the field nodes to the browser-based maintenance hub, where real-time actionable information is provided. This WiFi or LTE configuration can provide cloud-based support to all wireless nodes within 30m, making the architecture massively scalable. In addition, third-party sensors can also be wired into this gateway configuration.
ControlGate™ is the gateway to plant control systems for vibration and temperature nodes. This gateway configuration allows users quick integration into their control network via PLC/SCADA. Ethernet/IP or Modbus TCP/IP. In addition, third-party sensors can be wired into this gateway configuration.
ComboGate™ is a hybrid configuration of the CloudGate™ and ControlGate™ configurations. This option allows data to be securely delivered to both PLC/SCADA/DCS systems using. Ethernet/IP or Modbus TCP/IP as well as communication options for information transfers from the field nodes to the maintenance hub via the communication network. Information transfers from the field nodes to the maintenance hub via LTE or WiFi. Third-party sensors can be wired into this gateway configuration.
HOT SPOT MONITOR (HSM) is a hot spot monitor with a continuous, non-conductive temperature monitoring device. It detects potential hot spots and alerts personnel to abnormal electrical equipment. Integrating the HSM with a panel mount node will allow remote monitoring of the HSM data in the browser-based maintenance center.
To learn more about the products that can help you optimize your installations to automated or industrial monitoring systems, contact our representatives, they will be able to advise you adequately for your installations.
Blog posts
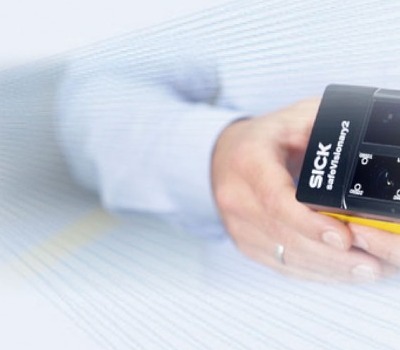
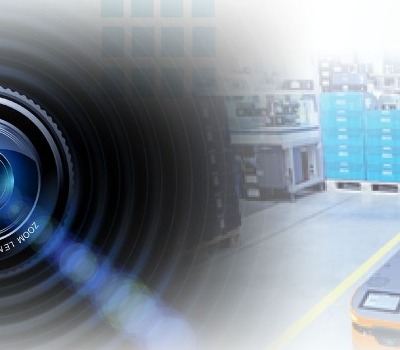
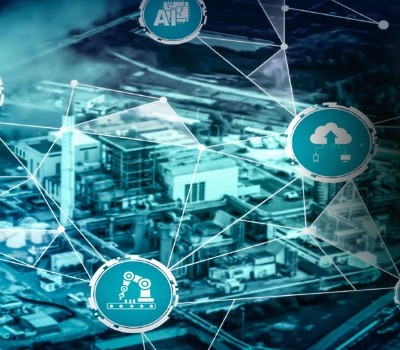
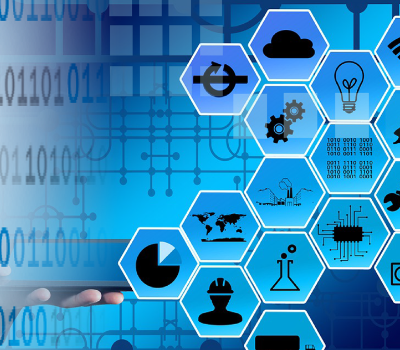