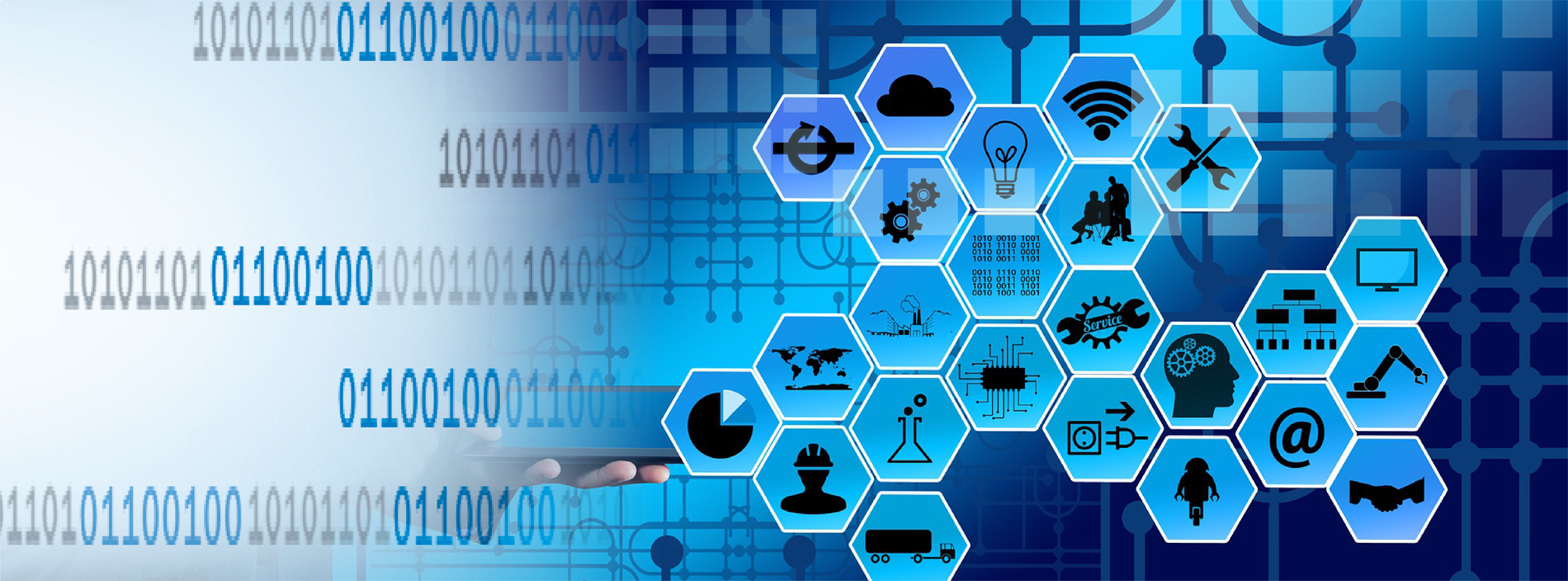
How IO-LINK works
Because there are many times when you need to find a way to efficiently connect hundreds or even thousands of intelligent sensors and actuators to collect data from operating systems, IO-Link is your best ally in maximizing your overall facility.
What is IO-Link?
IO-Link is a worldwide standardized technology. It enables communication between sensors and actuators. The system consists of an IO-Link master and an IO-Link device: a sensor, an actuator or a combination of both. IO Link is an interface that enables communication between control systems and so-called "low-level" components (sensors and actuators). This technology replaces parallel wiring of components, sensors and actuators to the control system. It also allows for the bi-directional exchange of a large amount of information. Among this information, we find cyclic and acyclic data.
IO-Link data types
The data link layer manages the data exchanged between the IO-Link master and the device. Messages (called M-sequences) containing process data, device data and event information are sent and received on a cyclic or acyclic basis, depending on the data type.
Cyclic data are:
Process data
Are the data from an IO-Link device transmitted cyclically approximately every 2 milisecond. during normal operation. The device specifies the size of the process data, with a maximum of 32 bytes available for input and output data.
The value states
When transmitting process data, the IO-Link device also sends a value status, which acts as a port qualifier or checksum. The value state data indicates whether the process data being sent is valid or not.
Acyclic data is:
Device data
Device data such as parameter values, device identification data and diagnostic information can be read and written to the device. As this data is not required permanently, it is exchanged on an acyclic basis on request from the IO-Link master. This reduces the communication bandwidth during normal operation.
The event data
When an event occurs, the device reports the event to the IO-Link master. The master then reads the event. Event data such as error messages and warnings (short circuit or overheating) or maintenance reminders (service required or lens cleaning) are only transmitted by the device on an acyclic basis.clique.
The technology offers multiple benefits:
-
Sensors and all peripherals can be integrated into all bus and automation systems in the same way. (Quick installation and parameterization)
- The technology is compatible with any standard equipment (2-wire or 3-wire sensors) in SIO mode (standard inputs/outputs)
- The system allows to communicate with the equipment at the lowest level
Signals are transmitted by voltage modulation through a standard asynchronous communication interface on unshielded cables -
Simple and quick replacement of sensors even for untrained personnel. The parameters are automatically stored in the device.
-
Reduction of the number of references and thus of the stock management
-
Access to all process data, diagnostic data, and device information (significantly faster data analysis)
-
Access to device-specific data, such as power supply, output status, contamination, etc.
-
End-to-end digital connection (no more conversion)
- Data transmission combines analog and binary signals
-
Analog signals are replaced by digital signals
-
Facilitate data feedback to the upper layer (modbus TCP, ethernet IP, Profinet, etc.)
-
Automatic resetting in case of device replacement during operation:
-
Reduction of downtime
-
Device replacement by unqualified personnel without additional tools
-
Avoidance of errors in re-setting
-
Depending on your applications and uses, there are many configuration and adaptation possibilities to optimize your installations. Contact our representatives for any questions regarding products using IO-Link technology. They will be able to advise you adequately for all your company's projects.
Contact details of team members
Blog posts
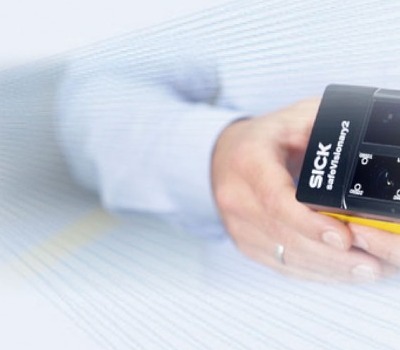
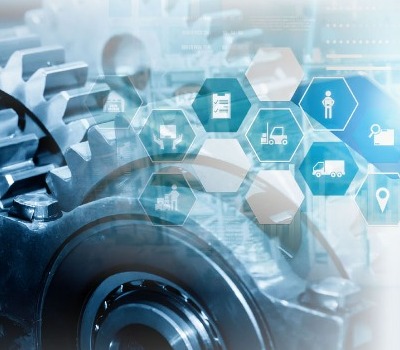
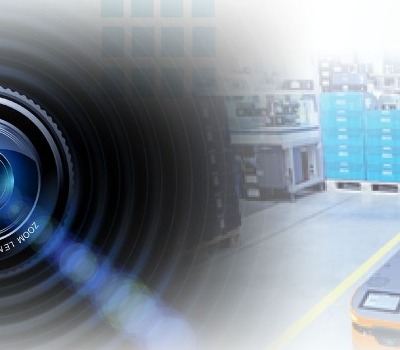
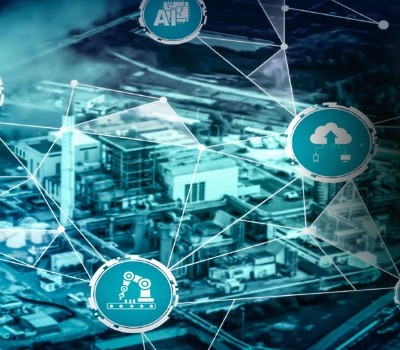