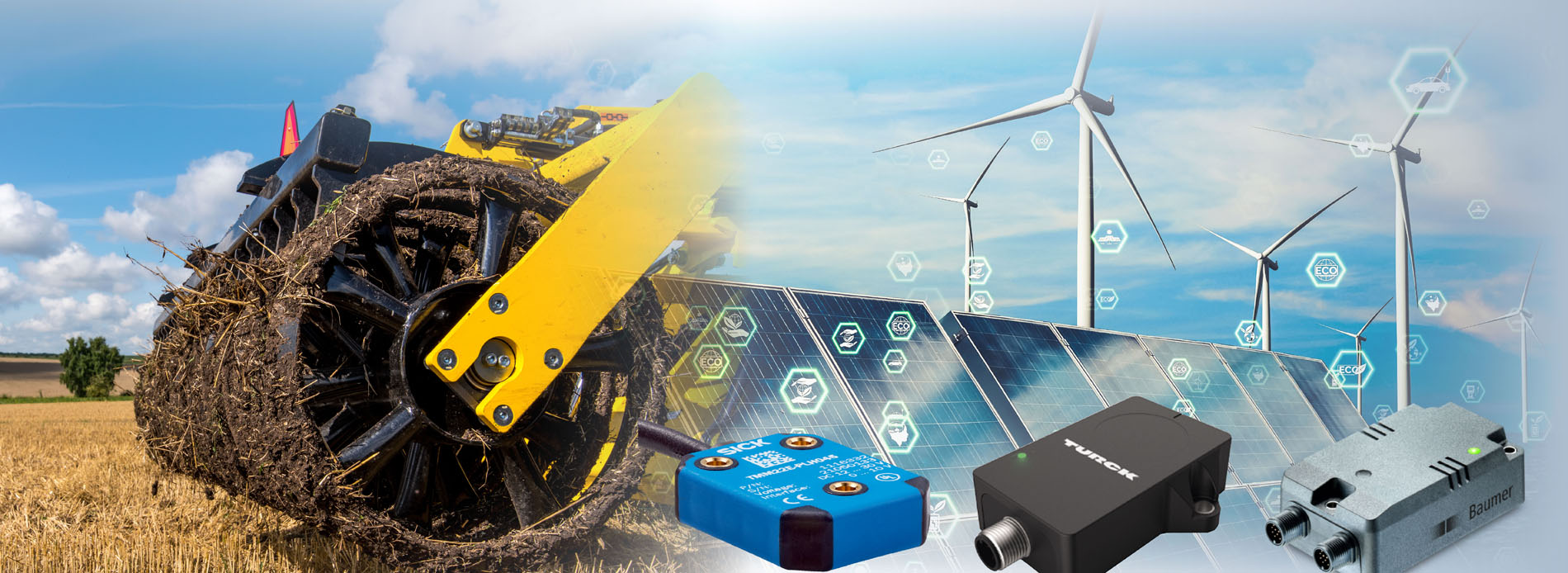
Introduction to static and dynamic MEMS inclinometers
What is an inclinometer?
By definition, an inclinometer (or clinometer) is a sensor that measures angles to the horizon (or horizontal). Where a bubble level (or level) allows you to detect precisely where the horizontal line is located, the inclinometer determines in addition the angle of inclination in relation to this horizontal line. It allows you to measure with precision and accuracy precise elements related to your installations or projects. It also has other important features that will save you a lot of time in your daily operations.
Here are some examples of use depending on the type of inclinometer:
-
As a measuring instrument with transverse sensitivity and output type proportional to the angle/sine of the angle
-
As a simple pendulum where the sensor is passive. The needle is integral with the pendulum and indicates the inclination by sliding on a dial.
-
In the form of a galvanometer where it becomes a mechatronic system device - Silicon or MEMS inclinometer. The sensor is formed by a sensitive element and another electronic element of conditioning of the signal. The sensitive element is a micro-machined system on silicon, generally made of a capacitive comb deforming according to the action of gravity.
-
In the form of a compass or a geometer with an inclinometer (the folding pin defines a straight line tangent to the housing opposite the zero point).
-
It can be used to monitor structures, road construction (inclination in curves...), the surveyor uses it as a slope indicator to measure the declivity of a land or to deduce by trigonometry the approximate height of distant buildings or trees, or allows to refuse functions to a construction vehicle which would be on a slope too inclined.
If you are considering an inclinometer, there are several factors to consider when choosing your product. Here are the criteria not to be ignored.
-
Precision
-
Gain
-
Offset
-
Noise
-
Sensitivity to the transverse axis of microelectromechanical systems (MEMS) devices
In addition to these criteria and depending on the applications to which the inclinometer will be dedicated, several performance criteria should be considered when making your choice.
The number of axes in the device is the first important indicator to consider. Depending on the application and system requirements, one can choose a one, two or three axis device. The offset/bias and gain of the sensor as well as their drift over time and temperature are of great importance.
Sensor resolution is another important performance measure. It depends on the noise, bandwidth, filtering and ADC (analog-to-digital conversion) resolution of the device. High noise sensors may require additional calibration, depending on the accuracy requirements of the application.
The stability of the offset and sensitivity as a function of temperature determines the accuracy of the sensor. Accuracy also depends on the vibration rectification error (VRE). DC rectification of broadband AC vibrations can shift the offset of the inclinometer, which can result in large errors.
The operating temperature range and whether the interface is analog or digital may also be important in some applications. Other performance specifications include offset/sensitivity calibration error, post-solder drift, transverse sensitivity, and nonlinearity. These characteristics may be less relevant because they can be measured and addressed by a post-assembly calibration at room temperature. This calibration is often necessary for a high accuracy inclinometer.
For many applications, the cost of a sensor will often go hand in hand with these key parameters. Because full calibration and adjustment requires additional time and equipment during manufacturing, higher performance devices typically cost more.
Accuracy is the closeness of the output of the device to the actual value. The closer the output is to the actual value, the higher the accuracy.
There are 2 types of inclinometers; static and dynamic
Static tilt measurement
Static tilt is the effect of the Earth's gravity (g = 9.81 m/sec² or 32.2 ft/sec²) on the axes of interest of the sensor. An accelerometer measures the projection of the acceleration due to gravity onto the sensor axes. However, in a real-world scenario, an inclinometer may also measure external acceleration, noise, and device offset. The impact of these components on the measurement of gravity effects must be negligible to obtain an accurate tilt calculation. If these external events are significant, the measured data must be compensated accordingly.
A MEMS-based accelerometer or inclinometer can be used to measure the tilt of an object relative to a horizontal plane. The sum of the forces measured on the three axes is equal to the force due to gravity (1g). Once these projections are obtained, basic trigonometric equations can be used to calculate the tilt angle with respect to each axis. Rotation of the object changes the magnitude of the sensed acceleration as a function of the sine of the tilt angle (α) between the sensing axis and the horizontal plane.
Dynamic tilt measurement
Dynamic tilt is the inclination and slope of an object's position when it undergoes rotation, vibration, motion, and shock, in addition to the earth's gravity.
Measuring dynamic tilt is more complex than measuring static tilt. The solution must include an accelerometer to determine the gravity vector and a gyroscope to measure the rotation of the object at the same time..
A MEMS-based dynamic inclinometer integrates both a three-axis gyroscope and a three-axis accelerometer for real-time tilt measurement. In scenarios where the accelerometer data is affected by external acceleration interference, a three-axis gyroscope provides angular velocities around the three x, y, and z axes. This compensates for the interference. However, gyroscopes inherently suffer from a slight drift in output data over time.
Applications of inclinometers
MEMS inclinometers are used in many applications because of their high time and temperature stability, cost-effectiveness, low power consumption and small size. MEMS static inclinometers are also easy to integrate, and they offer long-term reliability in addition to their technical and financial advantages.
Inclinometers are used to monitor the condition of structures, prevent vehicle rollover, in robotics or for precise positioning of antennas and platforms.
They are also used for predictive monitoring in the field of structural health (SHM). The goal being to identify potential problems before the structure collapses. Structural health monitoring sensors collect data over long periods of time to provide information on the overall condition of the structure.
Field of application:
Industry
-
Horizontal alignment of machine frames
-
Sizing of active or passive solar collectors: used to measure the masks that shade the sun. The mask is then transferred to the apparent path of the sun.
Construction and public works
-
Monitoring of structures
-
Road construction (inclination in curves...)
-
The inclinometer makes it possible to refuse functions to a construction machine which would be on a too inclined slope
Scientific and industrial research
-
Positioning of horizontal devices
-
Measurement of inclinations of the studied systems
Military
- Measurement of the inclination of the turret of a tank before firing
Marine
-
External inclinometer on a ship
-
At sea, it is used to measure the transverse inclination (heel) of a ship.
They can also be used in the fields of astronomy, ophthalmology, mountaineering, geology, meteorology, speleology and forestry.
Among the products available on the market, here are some that use MEMS technology and that have caught our attention.
The Sick TMS/TMM22 tilt sensor
The TMS22 (single-axis) and TMM22 (dual-axis) tilt sensors provide cost-effective, high-precision tilt measurements (± 0.25°). The measured values are transmitted as a linearized analog signal. They offer measuring ranges of up to 360° (1 axis) or ± 90° (2 axes). Their wear-free MEMS technology ensures consistently high accuracy and signal quality. They are wear-free, particularly durable, maintenance-free and insensitive to vibration and shock. They have preset functions for resetting during installation and their analog interfaces are customizable.
They can be used in the following application areas: photovoltaic and solar thermal energy, mobile agricultural and forestry machines, vertical bearing systems, crane and lifting equipment technology, driverless transport systems, construction machines and special vehicles as well as wind power plants.
Highly dynamic inclinometers for high-speed control circuits from Turck
With its new generation of inclinometers, Turck has combined accelerometer (MEMS) technology with gyroscope technology, so that shocks and vibrations can be masked much more effectively than with conventional signal filters. It is easy to mount thanks to its bubble level function, and the dynamic tilt signal allows for improved productivity at faster cycle speeds on moving or vibrating machines. In addition, it is very cost effective as IO-Link provides a fast output signal making shielded analog cables unnecessary.
They can be used for positioning and balancing applications or for dancer arm monitoring in the textile, printing or packaging industries. They can also be useful in the automotive industry, machine building and logistics.
Baumer Vibration / Acceleration Sensors
Baumer's vibration / acceleration sensors are a safe purchase for your company. They are ideal for the precise detection of acceleration, vibration and shock levels on machines or in your plant. They allow transmission of the measured acceleration values to the main controller via CANopen or an analog interface. It is easily integrated by means of a redundant safety relay output included in the safety system. It triggers when the default limit is exceeded. It allows a reduction of excessive vibrations before reaching critical amplitudes. These MEMS sensors are optimally accurate for minor deflections and minimal cross-talk between axes. In addition, user-configurable filters eliminate interference for even greater accuracy.
They are ideally suited for precise vibration monitoring, e.g. on wind turbine towers.
In conclusion, no matter which one you choose, MEMS inclinometers offer high performance and accuracy, high stability over time and temperature, and low power consumption, while being very cost competitive. They are very small and have low power consumption, making them an ideal choice for many applications.
For more information on any of these products or to talk to us about one of your optimization projects, contact one of our representatives, they will be able to advise you on the possible applications for your company or your project.
Contact details of team members
* Source
An Introduction to Static and Dynamic MEMS Inclinometers
By Jay Esfandyari & Tom Bocchinno, Related to : STMicroelectronics
Blog posts
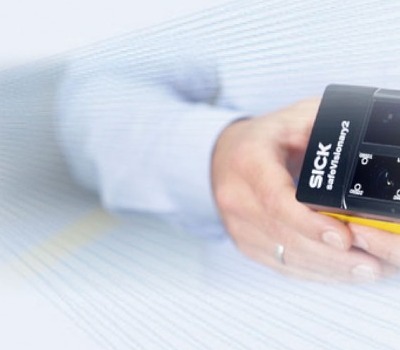
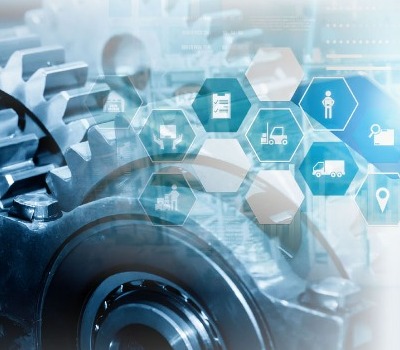
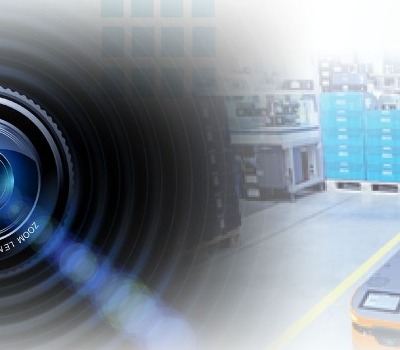
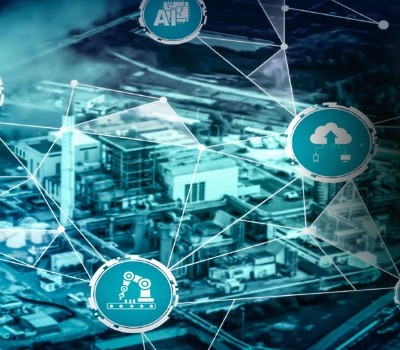