
La maintenance préventive, est-ce important pour votre entreprise ?
L’entretien préventif peut sembler élémentaire au premier abord, mais selon les statistiques, 55 % des entreprises exercent encore des méthodes de maintenance corrective. C’est une bonne pratique, puisque les systèmes de votre bâtiment fonctionnent jusqu’à ce qu’un problème ou une panne se produise. Il est par contre reconnu que ce type de maintenance engendre des coûts d’opération beaucoup plus élevés pour une entreprise.
Qu’est-ce que la maintenance préventive ?
La maintenance préventive est un processus essentiel pour assurer le bon fonctionnement de votre entreprise. Il s’agit d’une opération qui rallie surveillance et entretien préventif de votre matériel et de vos équipements. La maintenance préventive, ou maintenance technique planifiée, consiste à intervenir sur un équipement à intervalles réguliers ou en fonction de critères prédéfinis. Son objectif premier est de réduire les risques de panne sur les biens, machines et équipements, mais elle permet également d’atteindre des objectifs plus généraux. C’est pourquoi la plupart des usines et des entreprises cherchent à développer la part de maintenance préventive mise en œuvre par rapport à la maintenance corrective.
Quel est le but de la maintenance préventive ?
Le but premier de la maintenance préventive est de limiter le risque de bris et de réduire le nombre ainsi que la fréquence des pannes des machines. Elle est donc utile à :
- Réduire la fréquence des arrêts de production
- Diminuer les temps d’arrêt des machines pour la réparation
- Augmenter la durée de vie des machines et des équipements
- Prévoir les interventions de maintenance corrective afin d’offrir de meilleures conditions
- Mieux gérer les stocks des pièces de rechange
- Éviter toute consommation superflue d’énergie, de lubrifiant ou de consommables
- Réduire le budget de maintenance
- Améliorer les conditions de travail du personnel
- Limiter voire supprimer les causes d’accidents graves.
Pourquoi est-elle importante ?
Les temps d’arrêt étant l’une des principales pertes d’argent des entreprises. L’importance d’instaurer une maintenance préventive réside dans le fait qu’elle permet aux entreprises de poursuivre leurs opérations en continu, sans risques d’interruptions imprévues. La réduction des temps d’arrêt permet d’augmenter la productivité et d’améliorer la rentabilité de votre entreprise.
Faire une maintenance régulière de vos équipements vous permet aussi de réduire les risques de défaillance de l’équipement ou de réparations coûteuses. Grâce à la maintenance, vous pouvez donc conserver vos équipements en bonne condition et ainsi rallonger la durée de vie de vos machines.
Il existe 2 types de maintenance ; préventive et corrective. Quelle est la différence entre les deux ?
Pourquoi résoudre les problèmes lorsqu’ils surviennent quand l’on peut les prévenir ? La maintenance corrective vous permet de résoudre les problèmes alors que la maintenance préventive cherche à les éviter. Ainsi, la maintenance corrective, parfois divisée entre maintenance palliative et maintenance curative, est réalisée seulement au moment où une panne survient sur une machine ou un équipement. La maintenance préventive cherche quant à elle, au moyen de contrôles et de tâches de routine, à vérifier qu’une machine fonctionne correctement et à identifier d’éventuelles failles dans son fonctionnement avant que celle-ci ne tombe en panne.
Quels sont les différents types de maintenance préventive ?
Il existe 3 types de maintenance préventive :
- la maintenance systématique
- la maintenance conditionnelle
- la maintenance prévisionnelle.
La maintenance systématique
La maintenance préventive systématique est exécutée à des intervalles de temps préétablis ou selon un nombre défini d’unités d’usage, mais sans contrôle préalable de l’état de la machine. Elle concerne les premières étapes de dégradation sur une pièce d’un équipement. Elle peut être réalisée à intervalles prédéfinis, ou suivant un critère d’utilisation, sans prendre en compte les conditions d’utilisation de la machine.
Ce type de maintenance nécessite une bonne connaissance des règles de dégradation. Elle doit être réalisée de façon fiable, de manière à éliminer tout autre besoin de vérification supplémentaire entre deux interventions ou d’éviter une surveillance supplémentaire en dehors des périodes d’inspection.
Elle génère généralement des coûts peu élevés. Son seul inconvénient réside dans la nécessité de déterminer la fréquence idéale des remplacements de pièces. En voici quelques exemples : Le changement d’huile, de roulement, de joints, de ressorts, de contacts, de résistances, de lampes. Le réglage de tension, de courroie, de la pression, des potentiomètres. Le contrôle de niveaux, de couple, de serrage, etc.
La maintenance conditionnelle
La maintenance conditionnelle est basée sur une surveillance du fonctionnement de la machine et/ou des paramètres significatifs de ce fonctionnement incluant les actions qui en découlent (pression, niveau, débit, etc.). Les résultats de ces contrôles sont planifiés des opérations de maintenance industrielle. Ce type de maintenance permet de pallier les inconvénients d’une maintenance systématique. Elle ne requiert pas de connaissances supplémentaires, si ce n’est la comparaison des contrôles avec les seuils prédéfinis. Elle peut être continue avec un enregistrement permanent des paramètres relevés, ou discontinue avec une mesure périodique de ces paramètres.
La maintenance prévisionnelle
La maintenance prévisionnelle, aussi appelée maintenance prédictive, est conçue pour aider à déterminer l’état des équipements en service afin d’estimer quand la maintenance doit être effectuée. Cette approche promet des économies par rapport à la maintenance préventive de routine ou basée sur le temps, car les tâches ne sont effectuées que lorsqu’elles sont justifiées. Ainsi, elle est considérée comme une maintenance conditionnelle effectuée comme suggérée par les estimations de l’état de dégradation d’un élément. Elle est particulièrement utile pour prévenir les défaillances inattendues des équipements, augmenter la sécurité de l’usine, réduire les accidents avec un impact négatif sur l’environnement et d'optimiser la gestion des pièces de rechange.
La maintenance prédictive diffère de la maintenance préventive, car elle s’appuie sur l’état réel de l’équipement, plutôt que sur des statistiques de durée de vie moyenne ou prévue, pour prédire quand la maintenance sera nécessaire.
Maintenant, si vous souhaitez instaurer un système de maintenance préventive dans votre entreprise, le système de maintenance prédictif de GraceSense™ pourrait s’avérer une très bonne solution pour votre entreprise.
Le système de maintenance prédictive GraceSense™ est un système de surveillance de l’état des actifs qui utilise une technologie de capteurs sans fil intégrée. Les analyses de données avancées fournissent aux gestionnaires d’actifs des informations approfondies sur la santé des machines afin de prioriser efficacement les ressources et maximiser la valeur de leurs dépenses pour la maintenance. La technologie GraceSense™ améliore la fiabilité, la sécurité et les paramètres de maintenance en surveillant à distance l’état des équipements et en envoyant des notifications préventives par le biais d’alertes SMS ou e-mail avec des instructions de remédiation préconfigurées, étape par étape, lorsqu’un comportement anormal est détecté.
Il dispose d’une solution de maintenance conditionnelle sans fil rentable, capable de fournir un aperçu en temps réel, basé sur des capteurs, de presque toutes les applications industrielles. Les informations recueillies peuvent être exploitées afin d’aider à la prise de décision fournie dans le nuage via WiFi ou LTE et/ou dans l’automate via Ethernet/IP ou Modbus TCP/IP. L’application web simple et intuitive combinée au stockage sécurisé des données offre des possibilités illimitées pour la récupération, la visualisation, l’analyse et le rapport des données. La sécurité des travailleurs est donc améliorée, car elle permet de réduire les activités de maintenance correctives non planifiées.
Parmi les composantes du système pouvant être utile à votre installation ;
Le NŒUD PANEL-MOUNT™ est une solution rentable pour intégrer les capteurs tiers câblés via 0-10V, 4-20 mA, ainsi que des communications en série via RS485 à partir d’appareils tels que les téléphones portables, les ordinateurs portables, les ordinateurs de bureau, etc. Les Nœuds de capteurs sans fil peuvent surveiller les vibrations et la température afin d’évaluer de manière perspicace la santé des équipements rotatifs, les multiples options de montage garantissent un déploiement rapide dans les applications de tous les secteurs. Les batteries sont faciles à remplacer et offrent une durée de vie de 3 à 5 ans, selon l’utilisation.
Le système dispose également de 3 types de passerelles CLOUDGATE™, CONTROLGATE™, COMBOGATE™ pouvant transférer les informations accumulées sur les nœuds de terrain vers une plateforme de dépannage exploitable via le Cloud Maintenance Hub et/ou votre propre plateforme.
CloudGate™ transfère les informations des nœuds de terrain vers le centre de maintenance basé sur un navigateur, où des informations exploitables en temps réel sont fournies. Cette configuration WiFi ou LTE peut fournir une assistance basée sur le cloud à tous les nœuds sans fil dans un rayon de 30 m, ce qui rend l’architecture massivement évolutive. De plus, des capteurs tiers peuvent également être câblés dans cette configuration de la passerelle.
ControlGate™ est la passerelle vers les systèmes de contrôle de l’usine pour les nœuds de vibration et de température. Cette configuration de passerelle permet aux utilisateurs une intégration rapide dans leur réseau de contrôle via PLC/SCADA. Ethernet/IP ou Modbus TCP/IP. En outre, des capteurs tiers peuvent être câblés dans cette configuration de passerelle.
ComboGate™ est une configuration hybride des configurations CloudGate™ et ControlGate™. Cette option permet de fournir en toute sécurité des données aux deux systèmes PLC/SCADA/DCS en utilisant. Ethernet/IP ou Modbus TCP/IP ainsi que des options de communication pour les transferts d’informations des nœuds de terrain vers le concentrateur de maintenance via le réseau de communication. Les transferts d’informations des nœuds de terrain vers le concentrateur de maintenance via LTE ou WiFi. Des capteurs tiers peuvent être câblés dans cette configuration de passerelle.
MONITEUR DE POINTS CHAUDS (HSM) est un moniteur de points chauds avec un dispositif de surveillance de la température continue et non conductrice. Il détecte les points chauds potentiels et alerte le personnel en cas d’anomalie dans les équipements électriques. L’intégration du HSM à un nœud de montage sur panneau permettra de surveiller à distance les données du HSM dans le centre de maintenance basé sur un navigateur.
Pour en apprendre davantage sur les produits vous permettant d’optimiser vos installations vers des systèmes, automatisés ou de surveillance industrielle, communiquez avec nos représentant.es, ils seront en mesure de vous conseiller adéquatement pour vos installations.
Blog posts
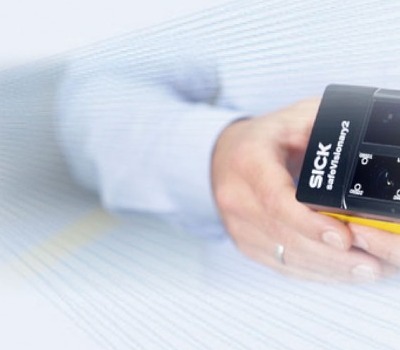
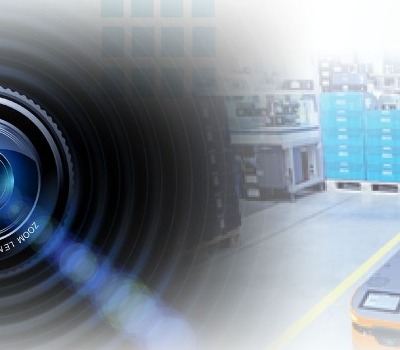
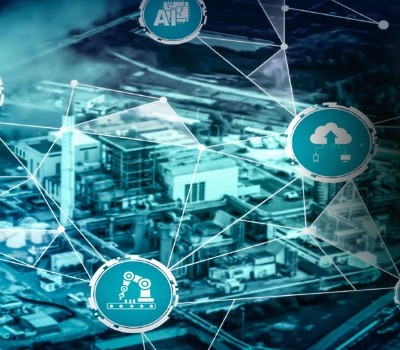
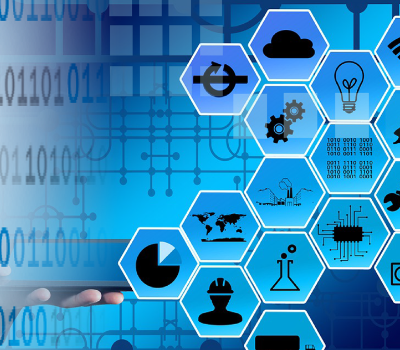